
The steel sector, new challenges and opportunities
Steel represents the essential element of infrastructure. Thanks to its high strength and ductility, it is used in a wide range of applications - from construction and infrastructure to transportation, household appliances, packaging, and the chemical and petrochemical industries.
STEEL PRODUCTION METHODS: BLAST FURNACE VERSUS ELECTRIC ARC FURNACE
The most commonly used steelmaking processes are the Blast Furnace (BF) and the Electric Arc Furnace (EAF). The blast furnace is a large industrial plant that, once commissioned, must run continuously. The raw material is iron ore, which is first converted into liquid pig iron at extremely high temperatures with the addition of carbon coke1. This is then refined to remove excess carbon and impurities to produce steel.
THE ELECTRIC ARC FURNACE: FLEXIBILITY AND ENERGY EFFICIENCY
The electric arc furnace, on the other hand, is a more flexible and energy-efficient solution. It is smaller and can be started up and shut down more quickly. The primary input is scrap iron, which is melted down to produce crude steel, then subjected to further refining processes.
PREVALENCE OF STEEL PRODUCTION METHODS IN ITALY AND WORLDWIDE
Today, about 71% of the world's steel is produced in blast furnaces. In Europe, however, production is more evenly distributed, with blast furnaces accounting for 55% and electric arc furnaces (EAFs) for 45%. Italy stands out with a clear predominance of EAFs, which are used for 86% of total domestic production2.
WHY ELECTRIC ARC FURNACES ARE MORE SUSTAINABLE THAN BLAST FURNACES
Both production methods involve melting iron, but the electric arc furnace offers a more sustainable and energy-efficient alternative. EAFs primarily use recycled ferrous materials as input, supporting a circular economy and reducing environmental impact. In addition, EAFs operate at lower temperatures and, as mentioned above, do not require continuous operation, resulting in lower energy consumption compared to blast furnaces and therefore lower emissions.
GREEN STEEL AND CO₂ EMISSION REDUCTION: THE TRANSITION OF THE STEEL INDUSTRY
The steel industry is currently responsible for an estimated 7-9% of global carbon dioxide emissions3. As pressure mounts on the sector to reduce its carbon footprint, industry players are increasingly investing in technologies aimed at reducing emissions and enabling the production of “green steel”.
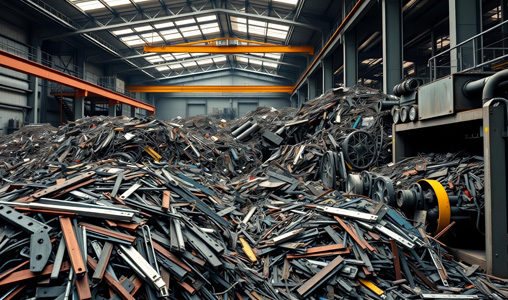
GREEN STEEL PRODUCTION TECHNOLOGIES: CCUS AND DRI
Among the leading technologies supporting green steel production are Carbon Capture, Utilisation and Storage4 (CCUS) and the use of Direct Reduced Iron5 (DRI), where hydrogen replaces gas as the chemical reactant.
Currently, most DRI production uses natural gas to remove oxygen from iron ore, but the process can also be driven by hydrogen, both as an energy source and as a reducing agent. Hydrogen-based DRI/EAF technology is considered the only viable large-scale solution for green steel production - provided that the hydrogen used is "green", i.e. produced from renewable sources.
INVESTMENT AND SUSTAINABLE SUPPLY CHAINS FOR DECARBONISING THE STEEL SECTOR
The main challenge for the deployment of decarbonisation technologies is the high investment costs required to implement such facilities.
Equally important is the development and securing of sustainable supply chains, particularly in relation to the extraction, transport and processing of materials. It is essential that all stakeholders along the supply chain work together to ensure that the entire production process is environmentally friendly and designed to minimise overall emissions’ impact.
Finally, securing a supply of clean energy is essential. Not only by sourcing renewable energy, but also by ensuring that national grids are able to provide sufficient power to run the facilities.
TOWARDS NET ZERO: THE GREEN TRANSITION OF THE STEEL INDUSTRY
The decarbonisation of the steel sector - one of the “hard to abate” industries - requires a coordinated effort from steel producers, supply chain operators, regulators and financial institutions alike to achieve net zero greenhouse gas emissions by 2050.
The steel industry must therefore accelerate its transition to a low-carbon future by investing in the development of new decarbonisation technologies.
Intesa Sanpaolo supports this transition, in line with its commitment to reach Net Zero by 2050.
INTESA SANPAOLO'S COMMITMENT TO A SUSTAINABLE FUTURE
IMI Corporate & Investment Banking Division is increasingly focused on sustainability and green innovation, supporting both the Italian and international economy. Combining ESG expertise with in-depth knowledge of sectors and financial products, it is well positioned to support customers throughout the process of developing and implementing sustainability initiatives.
1 Coke is a grey, hard and porous fuel with a high carbon content produced by heating coal or petroleum in the absence of air.
2 SOURCE: Federacciai Annual Report. "Italian steel industry.” Page 37
3 SOURCE: World Steel in Figures 2024. Page 2
4 CCUS is a technology that involves capturing carbon dioxide, typically emitted from large sources such as steel plants that use fossil fuels or biomass as fuel.
5 The DRI process is based on the direct reduction of iron ore using reducing gases or coal. The term “direct reduction” refers to the fact that the ore is not melted, but rather converted directly into a solid form. Reduced iron takes on a solid, porous structure, resembling a sponge.