
Il settore dell'acciaio tra nuove sfide e opportunità
L’acciaio rappresenta l’elemento portante delle infrastrutture. Le sue proprietà di alta resistenza e duttilità ne permettono l’utilizzo nelle più svariate applicazioni: dalle costruzioni alle infrastrutture, dai trasporti agli elettrodomestici, dagli imballaggi all’industria chimica e petrolchimica.
METODI DI PRODUZIONE DELL’ACCIAIO: CONFRONTO TRA ALTOFORNO E FORNO ELETTRICO AD ARCO
I metodi di produzione più utilizzati sono l’altoforno (Blast furnace, BF) e il forno elettrico ad arco (Electric arc furnace, EAF). Nel primo caso si tratta di un impianto industriale di notevoli dimensioni che una volta avviato deve operare in continuità. La materia prima utilizzata è il minerale di ferro che, con elevate temperature e l’aggiunta di carbon coke1, viene prima trasformato in ghisa liquida e successivamente privato del carbone in eccesso e di eventuali impurità per ottenere l’acciaio.
IL FORNO ELETTRICO AD ARCO: FLESSIBILITÀ ED EFFICIENZA ENERGETICA
Il forno elettrico ad arco rappresenta invece una soluzione più versatile ed efficiente, di dimensione più contenuta e che può essere avviato ed interrotto più rapidamente. In questo caso la materia prima è il rottame di ferro che viene fuso fino alla realizzazione di acciaio liquido e viene poi sottoposto a processi di raffinazione.
DIFFUSIONE DEI METODI PRODUTTIVI DI ACCIAIO IN ITALIA E NEL MONDO
Oggi circa il 71% della produzione mondiale di acciaio avviene tramite altoforno. In Europa invece la produzione è divisa quasi equamente tra altoforno (55%) e EAF (45%). In Italia c’è una netta predominanza del forno elettrico, il cui utilizzo è pari all’86% del totale2.
PERCHÉ IL FORNO ELETTRICO AD ARCO È PIÙ SOSTENIBILE DELL’ALTOFORNO
Entrambi i processi produttivi richiedono la fusione del ferro, ma l’utilizzo del forno elettrico rappresenta una soluzione più sostenibile e a maggiore efficienza energetica. Nel forno elettrico, infatti, la materia prima impiegata è materiale ferroso riciclato, che garantisce quindi circolarità, riducendo l’impatto sull’ambiente. Inoltre, il processo produttivo richiede temperature inferiori e, come già anticipato, non necessita di operare in continuità, generando così un risparmio energetico rispetto all’altoforno e, di conseguenza, minori emissioni.
ACCIAIO VERDE E RIDUZIONE DELLE EMISSIONI DI CO₂: LA TRANSIZIONE DELL’INDUSTRIA SIDERURGICA
Attualmente l’industria siderurgica è responsabile di una percentuale compresa tra il 7 e il 9% delle emissioni globali di anidride carbonica3 e il settore sta ricevendo un’attenzione sempre più crescente affinché riduca il proprio impatto emissivo, spingendo i player del settore ad investire su tecnologie che possano mitigare e diminuire le emissioni prodotte e generare “acciaio verde”.
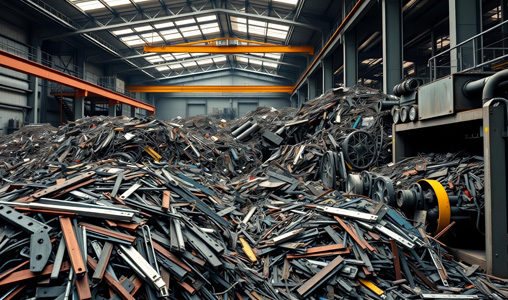
TECNOLOGIE PER LA PRODUZIONE DI ACCIAIO VERDE: CCUS E DRI
Tra le principali tecnologie a supporto della produzione di acciaio verde figurano il CCUS4 (Carbon Capture Utisation and Storage) e l’utilizzo del DRI5 (Direct Reduced Iron) con l’impiego dell’idrogeno al posto del gas come reagente chimico.
Oggi la maggior parte della produzione di DRI utilizza gas naturale per eliminare l’ossigeno dal minerale di ferro ma la tecnologia consente anche l’utilizzo dell’idrogeno, sia come fonte di energia che come agente riducente. La tecnologia DRI/Forno elettrico basata sull’idrogeno è ritenuta l’unica soluzione realizzabile su larga scala per la produzione di acciaio “verde”, a patto che lo stesso idrogeno impiegato sia verde, ovvero prodotto da fonti rinnovabili.
INVESTIMENTI E APPROVVIGIONAMENTO SOSTENIBILE PER LA DECARBONIZZAZIONE DEL SETTORE SIDERURGICO
La principale sfida all’applicazione delle tecnologie che sostengono la decarbonizzazione è il costo degli investimenti richiesti per l’implementazione degli impianti.
Resta fondamentale poi garantire e sviluppare catene di approvvigionamento sostenibili, soprattutto per quanto riguarda l’estrazione, il trasporto e la lavorazione dei materiali. È importante che tutti gli attori lungo la catena di approvvigionamento operino di concerto per garantire che l’intero processo produttivo sia green e improntato a ridurre l’impatto emissivo generale.
Infine, è essenziale assicurare una fornitura di energia “pulita”. Non si tratta solo di ottenere energia da fonti rinnovabili ma anche di verificare che le reti nazionali siano in grado di fornire sufficiente energia per alimentare gli impianti.
VERSO IL NET ZERO: LA TRANSIZIONE GREEN DELL’INDUSTRIA SIDERURGICA
La decarbonizzazione del settore siderurgico, che fa parte dei cosiddetti settori “hard to abate”, richiede sforzi congiunti da parte delle aziende produttrici di acciaio, degli attori dell’intera filiera produttiva, dei regolatori e degli istituti finanziari, al fine di raggiungere nel 2050 gli obiettivi del saldo netto delle emissioni di gas serra pari a zero.
L’industria siderurgica deve, quindi, accelerare la transizione verso un futuro a basse emissioni di gas serra, sviluppando nuove tecnologie per la decarbonizzazione del settore.
Intesa Sanpaolo promuove questo percorso, in linea con il proprio impegno a raggiungere il Net Zero entro il 2050.
L’IMPEGNO DI INTESA SANPAOLO PER UN FUTURO SOSTENIBILE
La Divisione IMI Corporate & Investment Banking si occupa sempre più di queste tematiche e degli sviluppi green, a supporto dell’economia e delle aziende italiane e internazionali e, combinando conoscenze specifiche relative ai temi ESG con competenze settoriali e di prodotto, è in grado di supportare la propria clientela durante l'intero processo di sviluppo e implementazione di iniziative di sostenibilità.
1 Il coke è un combustibile grigio, duro e poroso a base di carbone con un alto contenuto di carbonio. Si ottiene riscaldando carbone o petrolio in assenza di aria
2 FONTE: Relazione annuale Federacciai. “L’industria siderurgica italiana.” Pag. 37
3 FONTE: World Steel in Figures 2024. Pag. 2
4 Il CCUS è una tecnologia che prevede la cattura della anidride carbonica, generalmente proveniente da grandi fonti come gli impianti siderurgici che utilizzano combustibili fossili o biomasse come carburante.
5 Il processo del DRI invece si basa sulla riduzione diretta del minerale di ferro tramite dei gas riducenti o carbone. Si parla di riduzione diretta perché non avviene il processo di fusione ma si ottiene direttamente il prodotto allo stato solido: il ferro ridotto assume infatti una struttura solida e porosa, simile a una spugna.